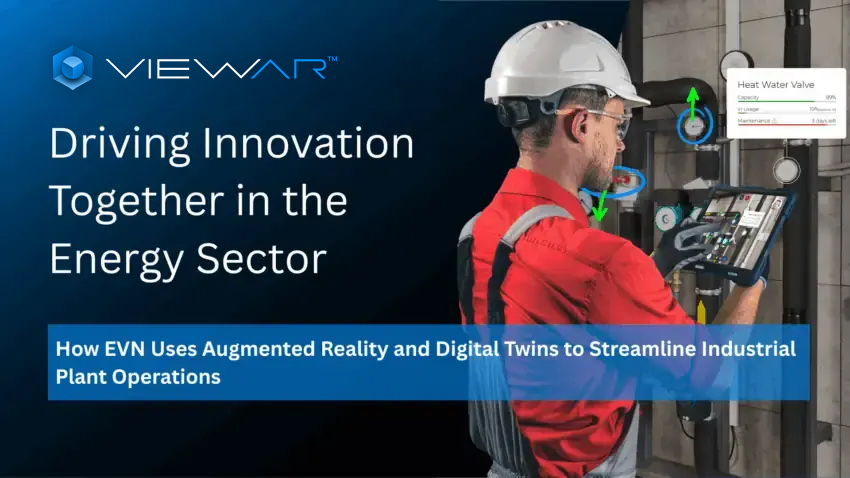
How EVN Uses Augmented Reality and Digital Twins to Streamline Industrial Plant Operations
Table of Contents
Introduction
EVN Group, is transforming plant operations through augmented reality maintenance. As one of Europe’s leading energy providers, EVN delivers electricity, gas, water treatment, and waste management services to over three million customers across 14 countries. EVN operates complex industrial environments so they’re consistently looking for innovative technologies to optimize operational efficiency, ensure safety, and reduce maintenance-related downtime.
At their Dürnrohr waste incineration plant in Austria, EVN faced significant challenges in tracking routine maintenance, managing unassigned issues like equipment damage, and streamlining incident visualization during daily briefings. That’s where ServiceAR from ViewAR stepped in—with powerful augmented reality (AR) capabilities and a fully integrated digital twin of the facility.
EVN’s Operational Challenges
Maintaining industrial-scale energy infrastructure is no small task. At Dürnrohr, EVN’s teams encountered several recurring issues:
- Manual incident reporting was inefficient, with frequent delays in logging and resolving issues like lamp failures or pipe leaks.
- Routine rounds and monitoring took longer than necessary due to unclear routes and scattered data.
- Morning briefings often lacked visual context, making it harder to align teams on current issues or site conditions.
- Keeping accurate as-built records post-revamps was labor-intensive and prone to human error.
🎥 See how EVN tackled these issues using ServiceAR
Watch the video below to get a quick look at how ServiceAR transformed daily operations at the Dürnrohr incineration plant.
To meet these challenges, EVN needed a solution that combined real-time spatial data, guided workflows, and seamless communication—while being scalable across multiple facilities.
How ServiceAR Solves These Challenges
ServiceAR, ViewAR’s enterprise-grade AR solution for industrial manufacturing, was implemented at Dürnrohr to bring efficiency, safety, and precision into EVN’s operations.
1. Incident Tagging
Employees can now localize and document malfunctions instantly via their mobile devices. A pipe leak? A broken light? Place a virtual marker, attach notes and images, and instantly share it with the relevant team—complete with a deep link for context-rich resolution.
2. Indoor Navigation
ServiceAR’s centimetre-accurate indoor navigation guides workers to exact locations within the plant. No more time wasted searching for assets—technicians are led straight to their task location, with full AR overlays providing real-time insights.
3. Workflow Support
Standard Operating Procedures (SOPs) have been transformed into interactive AR workflows. These visual guides reduce errors during complex maintenance and improve the efficiency of routine inspections and changeovers.
4. Digital Twin Integration
Perhaps most impressively, the entire Dürnrohr plant is now accessible as a digital twin, allowing teams—even off-site—to virtually “walk” through the facility via a browser. This has become a game-changer during morning briefings, where visual updates now replace verbal reports.
5. Seamless ERP Integration
ServiceAR integrates directly with SAP and IBM Maximo, enabling real-time data sync and eliminating manual duplication across systems. With support for deep linking and external databases, every incident and workflow is backed by up-to-date documentation and asset history.
Results: Faster, Smarter Maintenance
Since implementing EVN augmented reality maintenance workflows with ServiceAR at Dürnrohr, EVN has seen measurable improvements:
- Faster incident response with more accurate issue localization
- Streamlined daily operations, reducing time spent on routine tasks
- Improved communication and planning during team briefings
- Better documentation, especially post-maintenance or plant changes
These enhancements not only reduce operational costs but also increase safety and responsiveness—key priorities in the energy sector.
What This Means for Other Energy Providers
Whether you’re operating a power plant, a water treatment facility, or a gas distribution network, the challenges EVN faced are far from unique. AR-powered tools like ServiceAR can:
- Reduce unplanned downtime
- Standardize complex workflows
- Improve collaboration across teams and departments
- Enhance asset traceability and compliance
Contact us now and learn how ServiceAR supports energy providers with advanced spatial workflows, offline functionality, and ERP-ready integrations
Ready to Upgrade Your Plant’s Efficiency
If you’re looking to streamline operations, reduce downtime, and empower your workforce with cutting-edge AR technology, ServiceAR is the solution.
Book a demo today and discover how ServiceAR can transform your facility—just like it did for EVN.