Take incident tagging to a new level
ViewAR’s distinctive augmented reality technology enables precise reporting and effortless pinpointing of various incidents, such as damage to pipes and walls or broken machinery parts. While traditional reporting software allows incidents to be documented only through text and images, AR Incident Tagging also enables the preservation of the incident’s position in 3D coordinates. As a result, incident localization becomes seamless for both internal and external technicians, allowing them to easily navigate to any affected area using various mobile devices, such as smartphones, tablets, or AR glasses at any time.
Functionalities
Documentation
Effortlessly submit detailed incident reports from your mobile device, incorporating both images and text.
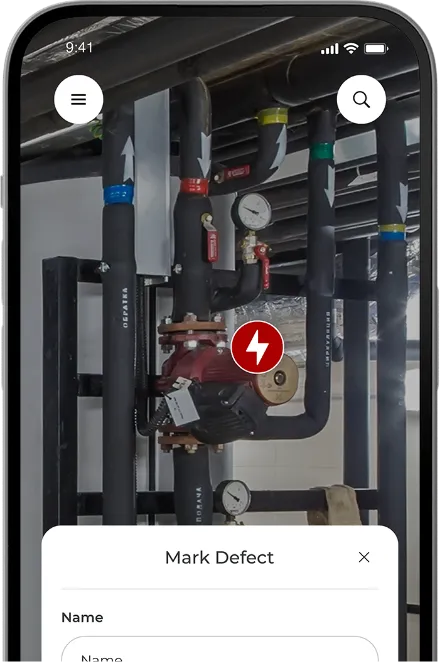
Positioning
When tagging an incident, the system automatically saves and integrates its position into the digital twin.
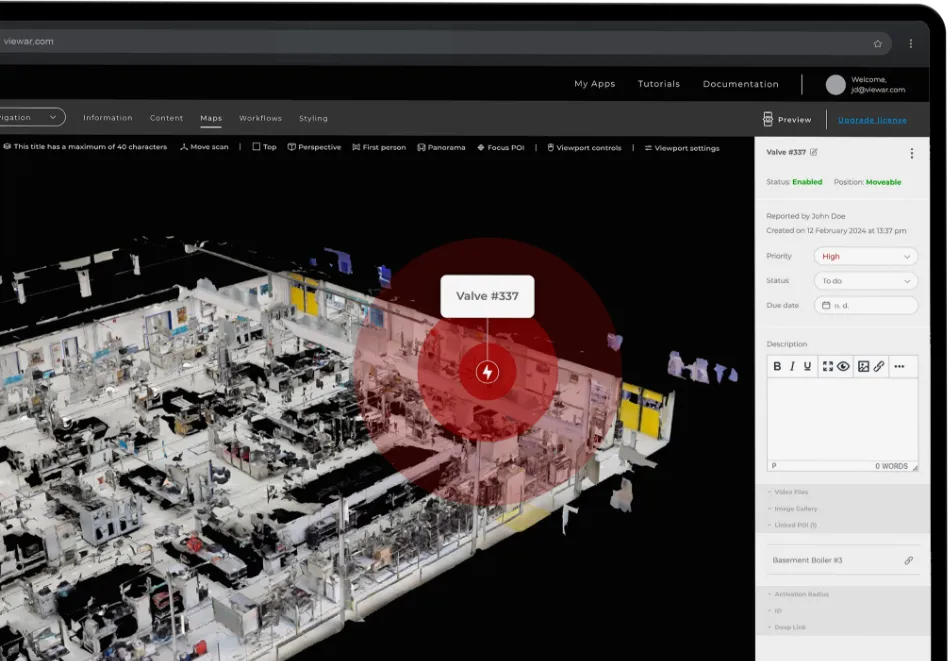
Integration
Easily integrate into established software platforms such as COMOS and SAP, or connect with any spreadsheet table based software (Excel, Google Spreadsheets, etc.) through REST API integration.
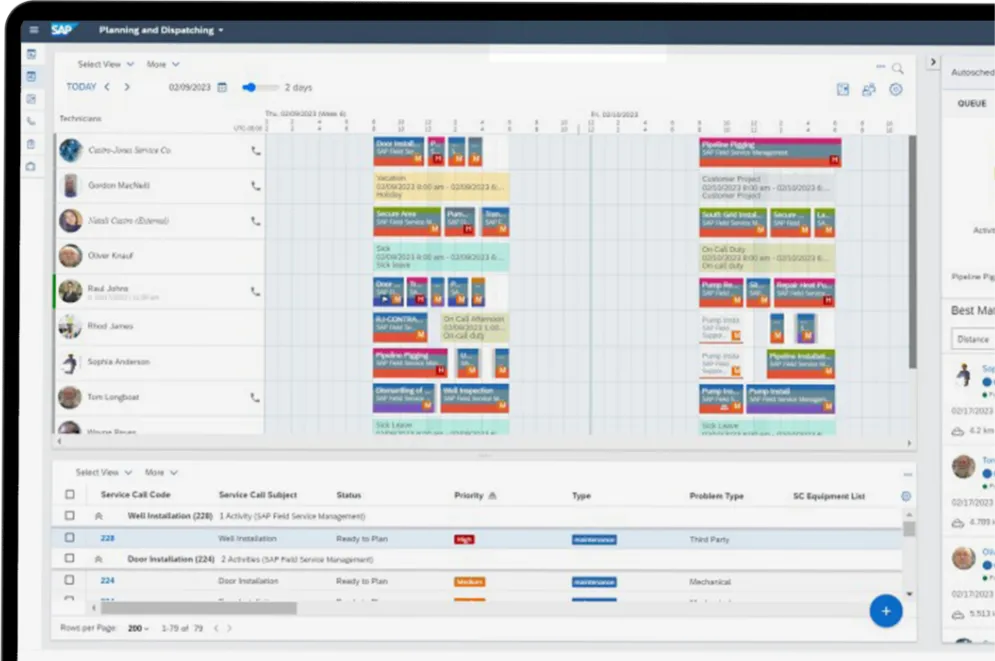
Localization
Use any AR capable mobile device such as mobile phone, tablet or glasses for visual guidance to navigate to the location of an incident.
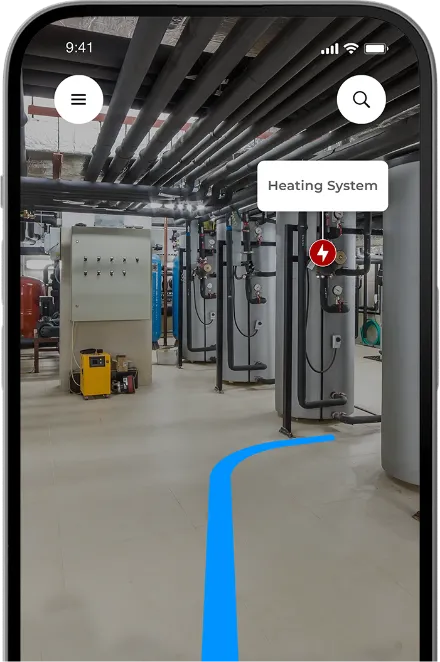
Benefits
Precise incident localization
Locating hidden or hard-to-reach damages is challenging. AR Incident Tagging helps to tag incidents within complex systems, making troubleshooting efficient.
Faster issue resolution
Documented incidents allow virtual inspections by stakeholders, aiding in the quick and accurate determination of necessary repair tools and equipment.
System integration
Integration with software and systems like COMOS and SAP via deep links or APIs, ensuring a seamless workflow with existing tools.
Enhanced collaboration
Encourages teamwork by enabling VR walkthroughs for incident examination in meetings or sharing with authorized colleagues.
Cost savings
Reduces costs from prolonged downtime and emergency repairs, enhancing overall cost-effectiveness and resource efficiency.
How it works
Report
Incidents can be tagged and documented with the help of a mobile device. When workers see an incident that needs to be reported, they can tag it by saving the location, taking a picture, and documenting the issue. Reported issues are collected, and technicians can be sent to solve the incident using the navigation and the documented information.
Plan
During the planning phase, planners can use their browser to open the web version and navigate through the facility. This helps them get a better overview and decide which equipment or tools might be needed on-site. For instance, if the incident is somewhere high up, scaffolding might be necessary, or specific safety equipment. Besides that, the web version helps to make meetings more efficient because the team can view everything virtually in their browser.
Execute
Within the execution phase, maintenance technicians are supported on-site with corrective maintenance measures. This starts with AR navigation, where technicians are guided to the right place of the damaged asset, to the usage of AR workflows and remote assistance which support the actual repair.