Where we can support
Asset Localisation
In fast-paced manufacturing environments, efficiency is key. ServiceAR optimizes the way your team identifies and locates the assets needed for the next production batch. With a vast inventory of assets to choose from, workers often spend valuable time searching for the right tools or materials. ServiceAR eliminates this inefficiency by overlaying precise location data and real-time guidance on the worker’s field of view, speeding up the setup process. By visually guiding operators to the correct assets, they can quickly select exactly what’s needed for each batch, ensuring a seamless transition from one task to the next. This means fewer errors, faster setup times, and improved operational productivity—every single time.
Maintenance Tours
Maximize the effectiveness of your maintenance tours with our AR solution, designed to enhance guidance and reporting throughout the process. Instead of relying on printed manuals or static digital displays, technicians receive dynamic, real-time instructions directly in their line of sight. Whether they’re performing inspections, tracking equipment status, or following up on routine checks, our AR technology ensures they stay on track, with step-by-step overlays that guide them through each task. Additionally, technicians can instantly document findings, log issues, and generate reports—all within the AR interface—making it easier to share critical information with managers in real-time. This seamless blend of guidance and reporting not only speeds up maintenance tours but also ensures that all data is captured accurately, reducing the potential for missed details and improving overall operational efficiency.
Production Changeovers
Production changeovers can be costly, with downtime often eating into valuable production time. ServiceAR helps mitigate these challenges by supporting your team through seamless changeover processes. With instant access to detailed instructions and equipment configurations via AR, your workers can quickly adjust to new production requirements, ensuring faster and smoother transitions. Whether switching between different product lines or adjusting machinery settings, AR provides workers with real-time guidance, reducing errors and minimizing setup time. By streamlining the changeover process, your facility can operate with greater flexibility, reduce production delays, and maximize throughput, helping you stay ahead of demand and improve overall efficiency.
Introducing ServiceAR
Empower your workforce with real-time access to information and step-by-step instructions, enhanced with the visual guidance of AR. ServiceAR is a powerful augmented reality solution designed for mobile devices, offering indoor navigation, streamlined workflow execution, and efficient incident tagging—all in one platform. Boost your team’s operational efficiency and reduce overhead. Try ServiceAR today and experience the future of workplace productivity.
Practical Use Cases
Reducing Planned Downtime for Product Changes
Location: US-Based Pharmaceutical Plant
The Challenge:
In a facility designed for small-batch manufacturing, maintenance teams faced significant challenges in preventive maintenance tasks. Changing membranes on automated valves required locating 20–40 specific valves among 9,000 on-site. This search accounted for 90% of the time spent on such work orders, delaying critical operations.
The Solution:
With ViewAR’s augmented reality navigation system, maintenance teams quickly identified and located the exact valves in a compiled work order. By leveraging AR for precise indoor navigation, the time spent finding valves was reduced by an impressive 60%, leading to faster task completion and minimized downtime.
Tag Incidents and Anomalies Immediately When They Are Detected
Location: EU-Based Energy Provider
The Challenge:
Identifying and documenting incidents in large plants often involves manual paperwork and delayed communication. Navigating to the exact location of the issue could take valuable time.
The Solution:
ViewAR enables maintenance teams to tag incidents at their precise location using AR, triggering automatic work orders for resolution. Technicians are then navigated directly to the affected area, significantly reducing the time spent searching for issues and improving communication across teams.
Monitoring and Root Cause Identification of Unplanned Shutdowns
Location: EU-Based Food and Beverage Company
The Challenge:
Unplanned shutdowns in production can be costly and disrupt manufacturing schedules. Identifying the root cause quickly is essential, but traditional methods of gathering machine data were inefficient and prone to delays.
The Solution:
ViewAR enables real-time monitoring of machines, displaying critical data such as rotation speed, power, temperature, and pressure directly on-site through AR. This provides maintenance teams with quick, actionable insights to identify the root cause of shutdowns. Step-by-step guidance ensures maintenance is compliant and accurate. With ViewAR, the time spent on root cause analysis was reduced by 20%.
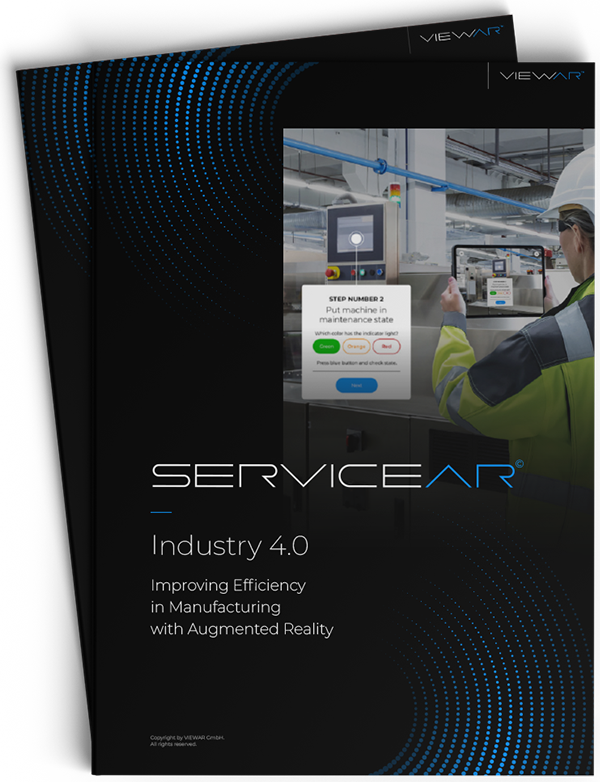
Improve Industrial Manufacturing with AR
Real-World Use Cases, Insights, Data, and Figures to Enhance Efficiency and Innovation