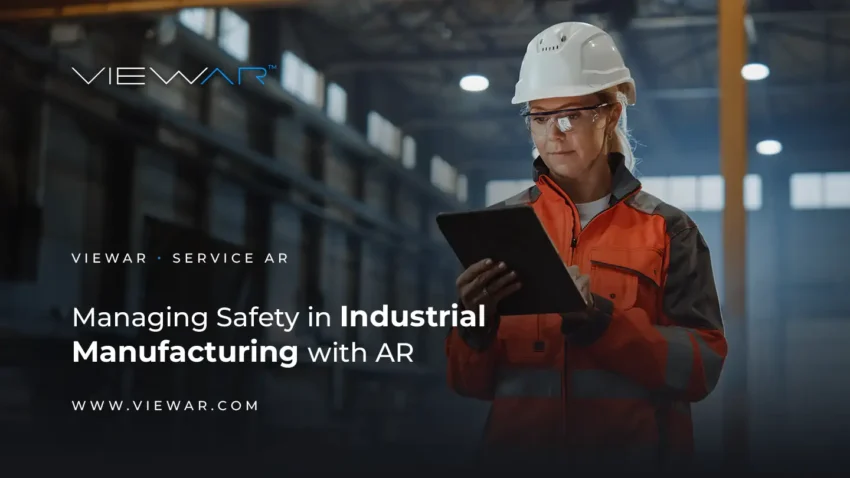
Managing Safety in Industrial Manufacturing with AR
Table of Contents
Introduction
Ensuring safety and reducing the risk of accidents in industrial settings is a crucial concern for companies and organizations in the manufacturing, construction, and other heavy industries. These industries often involve complex and potentially hazardous operations, and the risk of accidents and injuries is always present. Accidents and injuries can not only have serious consequences for individuals, but they can also impact productivity and profitability for businesses.

Current safety challenges in industrial manufacturing
Heavy machinery, potentially dangerous materials, and intricate procedures are all used in industrial manufacturing, which can provide a number of safety challenges. To ensure the health and wellbeing of their employees and the environment, industrial producers must regularly examine and reduce these safety concerns. The following are a few of the current safety issues in industrial manufacturing:
- Managing process related risks: One of them is making sure processes, such as the handling of hazardous materials and the management of process-related risks, operate safely and effectively. For the secure handling, storage, transportation, and disposal of hazardous items, businesses must have policies in place to make sure that the necessary requirements are met. Hazardous material handling especially calls for particular knowledge, abilities, and tools.
- Regular maintenance of machinery: Preventing accidents and injuries brought on by the usage of heavy equipment is also crucial. This includes making sure that the equipment is properly maintained, trained, and inspected. Maintaining equipment properly lowers the risk of equipment failure and the possibility for accidents and injuries by ensuring that it is operating safely and reliably. Before they can do any harm, it helps to recognize and get rid of potential risks including worn-out or defective parts, electrical problems, and fire threats.
- Exposure to chemical hazards: A major risk aspect is managing the proper handling, storage, and disposal of hazardous chemicals as well as safeguarding personnel from chemical exposure and limiting chemical discharge into the environment. The discharge of chemicals into the environment can have detrimental effects on the ecosystem and the communities nearby, and chemical exposure to employees can have catastrophic implications. Businesses must have policies in place for the secure handling and storage of dangerous chemicals, as well as for the prevention of chemical leaks and releases. This can entail using safety measures including proper ventilation and fire suppression systems, as well as gloves, respirators, and protective clothes.
- Managing safety protocols and procedures: Companies must have emergency response plans and protocols for events like fires, chemical leaks, and natural disasters in place. Managing them, keeping them up to date, and accessible at all times is crucial for worker safety but is one of the major challenges in safety management. In order to ensure that emergency response protocols are readily available in case of an emergency, it may be necessary to create both digital and physical copies of the plans and procedures. All employees, independent contractors, and other pertinent parties must have access to these copies, which must be kept current. The emergency response plans and protocols must be known to all employees, and frequent training on emergency response processes is required.
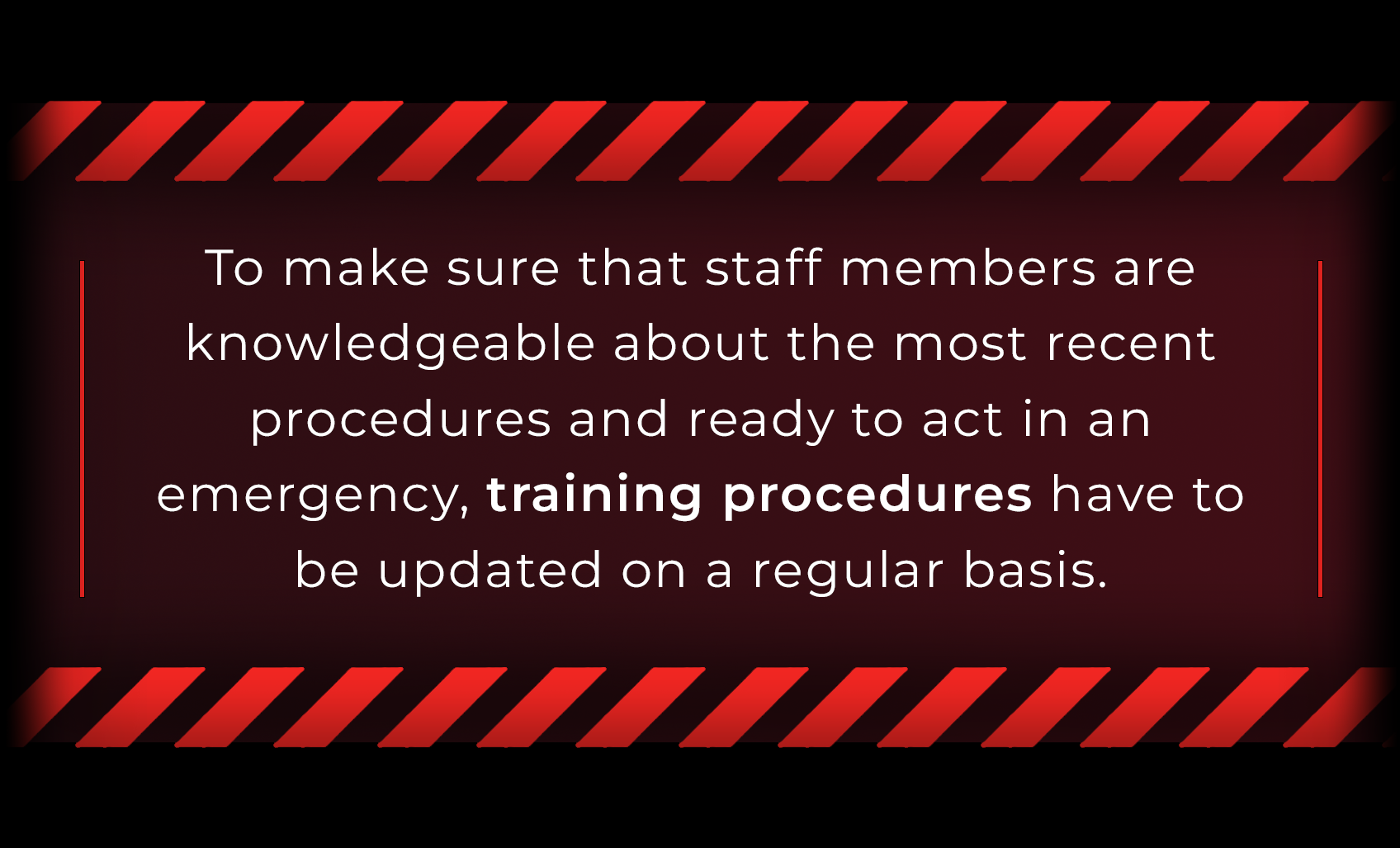
In industrial manufacturing facilities, the environment, worker safety, and worker health come first. However, this might present substantial difficulties because of the complexity of these facilities, the requirement for resources, the requirement to keep emergency plans current, the necessity for accessibility during emergencies, and the requirement for frequent training. Despite these obstacles, it is crucial for organizations to get through them to guarantee a secure workplace.
The augmented reality solutions
It is essential to implement effective strategies and measures to enhance safety and reduce the risk of accidents in industrial settings. Augmented reality (AR) has the potential to tackle that by providing workers with real-time information and guidance. Let’s highlight some of the main features how augmented reality can improve the safety of your workforce:
- Provide digital step-by-step instructions: Making mistakes can be a safety issue by itself. One way that VIEWAR can enhance safety in industrial settings is by providing workers with visual instructions and alerts. For example, AR can be used to display step-by-step instructions on the factory floor, helping workers to follow procedures more accurately and safely. Improve the communication of information by adding valuable digital notes and dynamic checklists to your digital work instructions to increase safety and reduce the risks of potential mistakes.
- Merge and visualize IoT-data: Another way that VIEWAR can enhance safety is by providing workers with real-time information on the status of safety systems. When there is too much data available, and your workforce cannot see the necessary data at the right place and time, it might become a safety issue. AR can be used to display data on the performance of safety equipment, such as personal protective equipment or emergency shutdown systems in a way that makes it easier to understand. This can help workers to identify and address potential problems before they become serious issues. AR can also be used to highlight potential hazards or danger zones, alerting workers to take extra caution in these areas.
- Improve quality of training and onboarding: Mistakes can hardly be made if the training and onboarding was done properly. An essential factor in increasing the safety of a company and its employees is therefore training. This should include the precautions to ensure safety in companies and address possible risks. In this way, the workforce can react in time to avoid potential damage. With the help of augmented reality, this challenge can also be solved easily! With a mix of digital workflows and remote assistance, the employee can learn from the digital recordings of SOP and call in an expert when needed – even if the expert is not available in the company at the time.
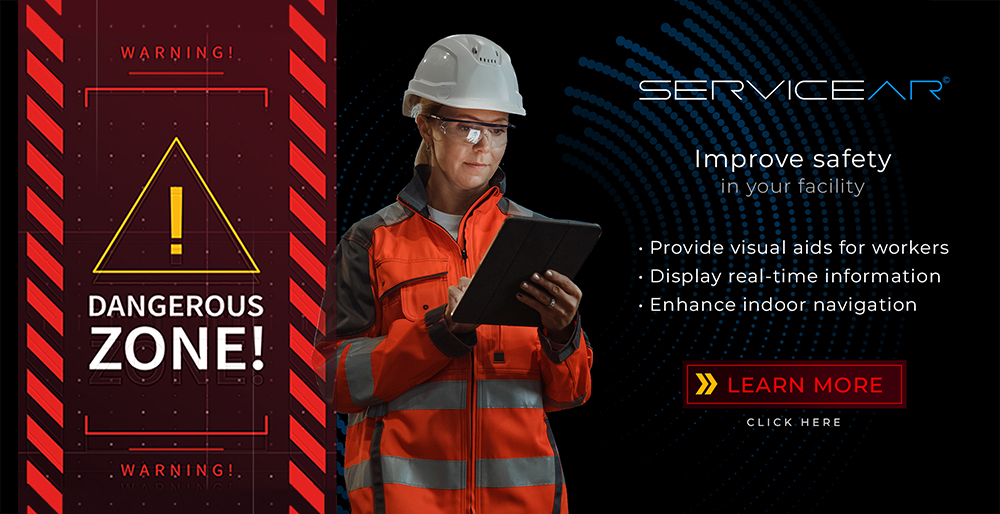
Conclusion
The use of augmented reality (AR) in industrial manufacturing has the potential to completely change how businesses approach safety. AR gives workers real-time, context-aware information and assistance that can help to reduce the hazards associated with difficult and dangerous tasks. AR can help to reduce the hazards associated with difficult and risky operations, protecting the safety and wellbeing of employees in industrial manufacturing environments by enhancing training and awareness and supporting workers in real-time.